Step into the Third Industrial Revolution!
Advanced 3D Printing, Digital Design, and 3D Fusion Manufacturing
Want to build a functional prototype or replacement part? ...We can help with that!
Want to make it real in Canada? ...We make everything in Canada!
What Our Customers Say
our 3D printing services
3D printing
We offer a host of 3D Printing, Rapid Prototyping, and Digital Production capabilities that are ready to meet your unique manufacturing challenges!
learn more →digital design
Optimized geometry and bespoke digital design. We specialize in design for additive manufacturing (DFAM).
learn more →3D fusion
3D Fusion is a novel additive manufacturing method used to improve the isotropic strength, quality, and structural consistency of as-built 3D printed parts.
learn more →our proven 3D printing process
To make a physical part or component “real” using 3D printing, you will need to do at least the first 2 of the 4 things prescribed below, depending on your usecase (application).
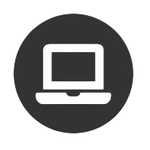
1. make it digital
All our 3D printing services require a digital model to begin and we are here to help every step of the way.
- Get 3D model (STEP or STL formats) of part(s)
- Part Analysis and Cost Estimates based on your model
- Optimize model using Design for Additive Manufacturing (DFAM) principles.
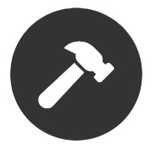
2. make it physical
Generating a physical part from a digital model is a prototyping process that we have perfected in our 10 years of experience.
- Print cost effective prototypes
- Validate physical outcomes and attributes associated with design
- Iterate as required to achieve optimized outcomes
- Develop project plan and budget (from prototype to fully scaled production)
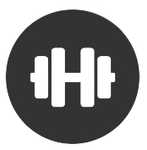
3. make it strong
Our innovative 3D Fusion process helps improve the strength in 3D printed parts.
- Select appropriate materials, platforms, and printer settings for fabrication
- Post Processing of 3D printed parts
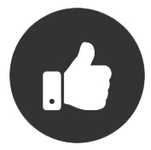
4. make it work
We use functional testing of the finished parts and iterate the design as needed to help make it real!
- Iterate process of design, print, and testing as required
- Develop strategies for scaled production
What is “it” you may ask? it is anything you can imagine! And we specialize in moving all kinds of “anythings” through the New Product Development Cycle. Let us apply our current, professional, and specialized knowledge of 3D printing and Hybrid AM to your unique manufacturing challenges. We can help you through any steps and stages of the process as you require, in order to Make It Real!
got a project?
make IT real!
We use 3D Printing combined with other novel and specialized AM methods to
make just about anything you can imagine!